In the vast world of industrial manufacturing, hot forging die steel plays a vital role. It is the core material for metal hot deformation processing, just like bones supporting the body and blood running through the body, injecting strong power into the development of modern industry.
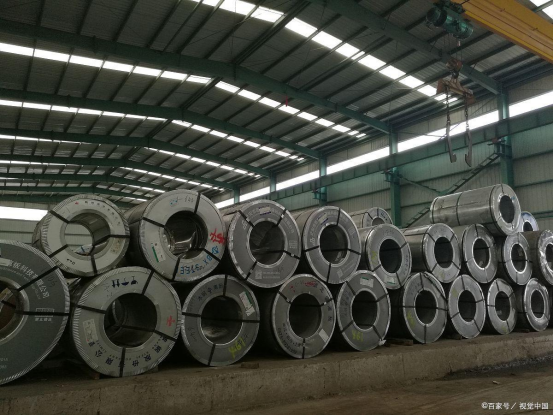
1. Characteristics of hot forging die steel: the industrial code of both rigidity and flexibility
The reason why hot forging die steel can stand out in the harsh environment of high temperature and high pressure.
High temperature hardness and red hardness: During the hot forging process, the surface temperature of the mold often rises to 400-500℃, or even higher. Hot forging die steel forms a secondary hardening effect by adding alloy elements such as tungsten (W), molybdenum (Mo), and vanadium (V), so that the material still maintains high hardness (HRC50-60) at high temperatures, avoiding mold collapse caused by softening.
Toughness and fatigue resistance: During the forging process, the mold needs to withstand huge impact force and alternating stress. Elements such as chromium (Cr) and silicon (Si) in hot forging die steel increase the phase transition temperature and enhance the ability to resist thermal fatigue, just like giving the mold “flexibility” to prevent cracking due to repeated heating and cooling.
Wear resistance and corrosion resistance: The friction between metal flow and the die surface requires the material to have high wear resistance. The high carbon content (0.3%-0.6%) and alloying design of hot forging die steel significantly improve its surface wear resistance and oxidation resistance, and extend the life of the die.
2. Types of hot forging die steel: material matrix based on the material
There are many types of hot forging die steel, forming a diversified material system to meet different working conditions.
General type representative: H13 steel
As a medium-grade hot working die steel commonly used in China, H13 has good heat resistance and corrosion resistance, and is suitable for small and medium-sized hot forging dies, copper alloy forging, etc. Its cost-effectiveness makes it the first choice for many companies.
High wear-resistant pioneer: LG/8566 steel
With a hardness of up to HRC54-60 and excellent wear resistance, it is particularly suitable for hot forging of stainless steel and high-temperature heavy-load molds. This type of material has outstanding anti-softening performance and is a “weapon” for meeting high wear resistance requirements.
Complex parts expert: GR steel
Designed for complex shapes and high toughness requirements, GR steel exhibits excellent performance in the fields of special equipment parts, shock-absorbing connectors, etc. Its good toughness can prevent brittle fracture of the mold under impact.
New material breakthrough: 8433/QRO90 steel
By optimizing the alloy ratio, the softening resistance of this type of material reaches 2-3 times that of H13, which significantly extends the service life of the mold. They are ideal for asymmetric deep pit parts and high temperature and heavy load molds.
3. Application of hot forging die steel: an all-round player in the industrial field
Hot forging die steel has a wide range of applications, covering almost all industries that require high strength, high hardness, high wear resistance and high heat resistance die materials.
Automotive industry: The production of engine parts, brake systems and suspension systems relies on hot forging die steel. For example, large and medium-sized stamping dies and die-casting dies need to withstand high temperatures and high pressures to ensure the accuracy and reliability of automotive parts.
Electronic and electrical industry: The demand for high-precision molds and plastic parts has promoted the application of hot forging die steel. The manufacturing of electronic products such as mobile phone shells and flat-panel TV shells cannot be separated from its good surface finish and dimensional stability.
Aerospace: Lightweight and high-strength hot forging die steel is used to manufacture complex-shaped dies and parts. Hot forging of materials such as aluminum alloys provides key support for aerospace equipment.
Plastic products industry: The high temperature and high pressure injection molding process places strict requirements on mold materials. Hot forging mold steel can withstand impact without deformation, ensuring the smoothness and precision of the inner surface of the mold.
4. The future of hot forging die steel: technology upgrade and market expansion
With the continuous advancement of industrial technology, hot forging die steel is moving towards high performance and long life.
Material upgrade: New hot forging steel (such as 8433) significantly improves softening resistance and service life by optimizing alloy ratio. In the future, more materials with excellent performance will be developed and applied.
Process innovation: The application of forging deformation quenching, surface strengthening (such as PVD/CVD coating) and other processes has further improved the performance of the die. These technological innovations will promote the development of hot forging die steel to a higher level.
Market growth: The global forging market continues to expand and is expected to reach RMB 725.4 billion by 2026. The hot forging die steel market has huge potential. With the advancement of domestic substitution for imports, the mid-to-high-end market will usher in more opportunities.
Hot forging die steel, the “bones and blood” of industrial forging, is injecting new vitality into the development of modern industry with its constantly innovative technology and wide application fields. In the future industrial arena, it will continue to play a key role and promote the manufacturing industry to a higher level.
Add comment