The differences between H13 electric furnace steel and electroslag steel are as follows:
Due to the different smelting methods, H13 electric furnace steel is compared with electroslag steel.
1. Electric furnace steel has poor density and low purity;
2. The annealed state has severe band segregation and the annealed structure is uneven;

3. A large number of liquid carbides do not change after quenching and tempering; in the impact test, cracks are prone to occur where chain-like liquid carbides gather, and transverse stripes appear on the fracture, resulting in lower toughness.
H13 mold steel application
Mainly used as hot forging dies, hot extrusion dies and aluminum alloy die-casting dies.
Chemical composition and function of H13 die steel
H13 steel belongs to C-CR-mo-si-v type steel, brand 4CR5MOSIV1.
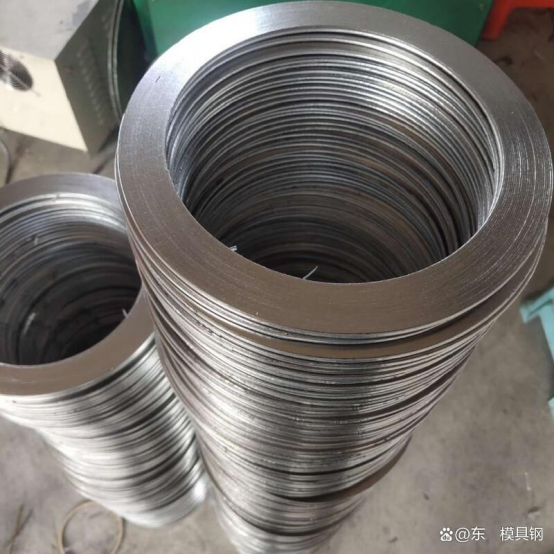
Carbon (C) is 0.32~0.45%, silicon (Si) is 0.80~1.20%, manganese (Mn) is 0.20~0.50%, chromium (CR) is 4.75~5.50%, vanadium (V) is 0.80~1.20%, molybdenum (Mo) is 1.10~1.75%, the allowable residual content of sulfur (S) is ≤0.030%, and the allowable residual content of phosphorus (P) is ≤0.030
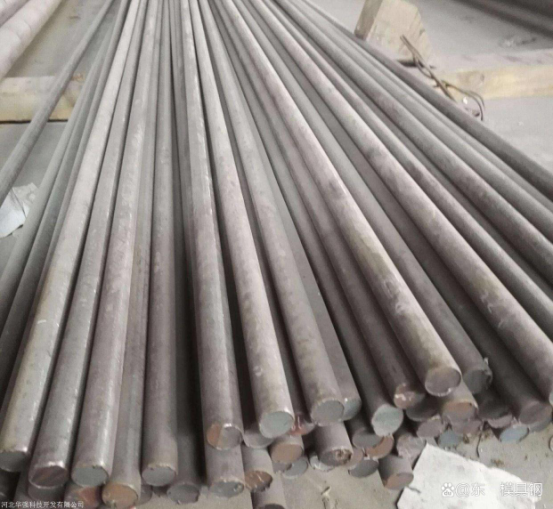
Some of the chemical components function as follows:
1. Increasing the carbon content in steel will increase the strength of the steel. For hot working die steel, it will increase the high temperature strength, hot hardness and wear resistance, but will lead to a decrease in its toughness. Therefore, the carbon content of the steel should be reduced as much as possible while maintaining strength.
2. Chromium has a favorable effect on the wear resistance, high temperature strength, hot hardness, toughness and hardenability of steel. At the same time, its dissolution into the matrix will significantly improve the corrosion resistance of steel.
Add comment