M42 High Speed Steel Strip: An All-Round Expert in the Industrial Field
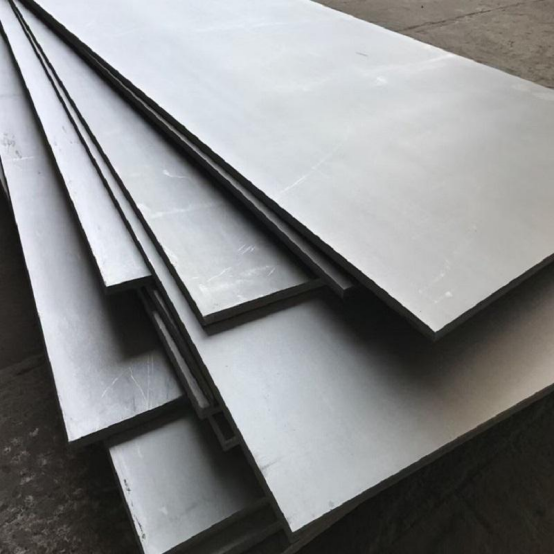
In the vast system of modern industry, M42 high-speed steel belt has become an indispensable key material in many fields due to its excellent performance. From precision machining to high-strength mold manufacturing to the aerospace field with extremely high requirements for material performance, M42 high-speed steel belt has left a deep mark. It is like an all-round industrial warrior. No matter what complex working conditions and stringent requirements it faces, it can show extraordinary strength and provide a solid guarantee for the efficient and stable operation of industrial production. So, what unique properties does M42 high-speed steel belt have? How does it play a role in different industrial scenarios? What is the secret of its production process? Next, let us explore the wonderful world of M42 high-speed steel belt together.
1. Understanding M42 High Speed Steel Belt
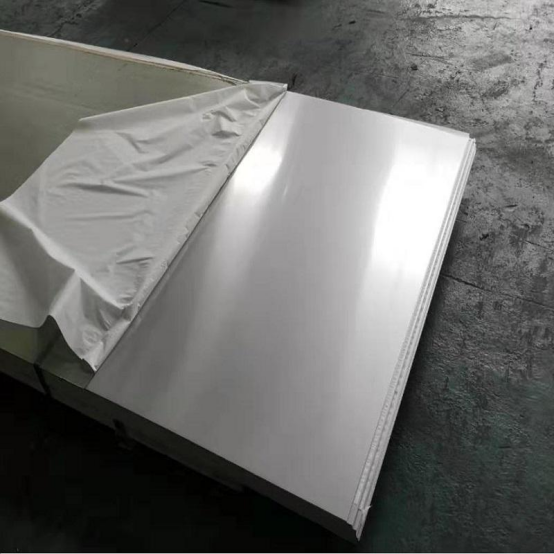
1. Unique ingredients create extraordinary performance
The chemical composition of M42 high-speed steel strip is like the cornerstone of its performance, and each element plays an indispensable role in it. Carbon (C), as one of the key elements that provide hardness, is usually between 0.90% and 1.05%. It enables M42 high-speed steel strip to have a hard tool edge and provides it with the necessary cutting ability in cutting processing. The addition of silicon (Si) and manganese (Mn) can improve the strength and hardness of the steel, while also enhancing its wear resistance. They work together in the steel to improve the overall performance of the steel strip.
Molybdenum (Mo) and cobalt (Co) are key elements to improve the performance of M42 high-speed steel strip. The content of molybdenum is generally 1.15% – 1.85%. It is an important alloying element to improve the hardness, wear resistance and thermal stability of steel. In high temperature environment, molybdenum can effectively prevent the softening of steel, maintain its hardness and strength, so that M42 high-speed steel strip can still maintain good performance in high-speed cutting and high-temperature processing. The content of cobalt is 9.00% – 10.00%. It can not only improve the toughness and wear resistance of steel, but also promote more carbides to dissolve in the matrix during quenching and heating, thereby further improving the hardness and wear resistance of the matrix. The addition of cobalt makes M42 high-speed steel strip perform well when processing workpieces with high hardness and high wear resistance requirements.
The content of chromium (Cr) is 3.50% – 4.25%, which can improve the corrosion resistance and wear resistance of steel, form a dense oxide film on the surface of the steel strip, prevent the steel strip from being corroded by the external environment, and extend its service life. The content of vanadium (V) is 0.95% – 1.35%, which can refine the grains, improve the hardness and wear resistance of steel, make the steel strip more stable during processing, and not prone to deformation and breakage.
(II) Overview of excellent performance
High hardness : After quenching, the hardness of M42 high-speed steel belt can reach 67-70HRC. Such high hardness makes its blade extremely sharp and can easily cut into various materials with higher hardness. In metal cutting, whether it is cutting steel, stainless steel or other high-strength alloys, it can show excellent cutting performance, greatly improving processing efficiency and processing accuracy.
Good thermal stability : M42 high-speed steel belt has excellent thermal hardness and can maintain high hardness and wear resistance in high temperature environment. When the tool surface generates high temperature due to friction during cutting, M42 high-speed steel belt will not soften as quickly as ordinary steel, but can still maintain stable cutting performance to ensure the continuity and precision of processing. This feature makes it particularly suitable for processing high-temperature materials, such as high-temperature alloys commonly used in the aerospace field.
Excellent wear resistance : Due to the effects of cobalt, molybdenum and other elements in its chemical composition, M42 high-speed steel belt has excellent wear resistance. Under high-speed cutting and heavy load conditions, it can effectively resist wear and maintain the cutting performance and life of the tool. Taking saw blades and drill bits as an example, saw blades and drill bits made of M42 high-speed steel belt can remain sharp for a long time when cutting hard materials, reduce the frequency of tool replacement, and reduce production costs.
Cutting stability : The uniform organizational structure and excellent cutting characteristics enable M42 high-speed steel belt to achieve a stable cutting process during cutting. In precision machining, it can produce high-quality machining surfaces, ensure the accuracy and quality of machined parts, and meet the needs of industries with extremely high requirements for product surface quality.
2. Wide application of M42 high speed steel belt
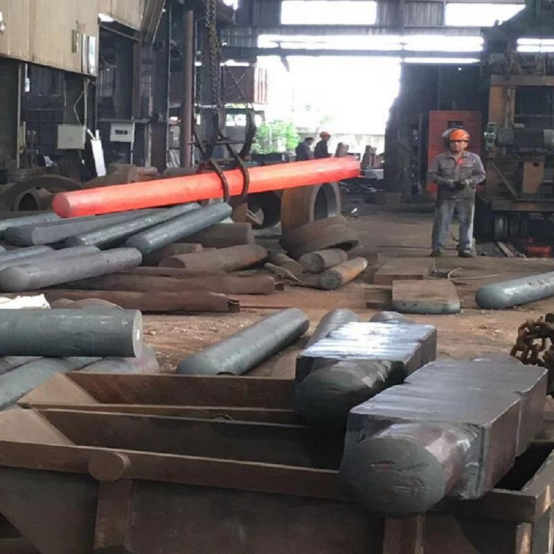
1. Cutting tools: the core of efficient machining
In the field of metal processing, cutting tools are the key to achieving efficient and precise processing. M42 high-speed steel strip has become an ideal material for manufacturing cutting tools due to its high hardness, good thermal stability and excellent wear resistance.
In automobile manufacturing, the processing of engine cylinders, crankshafts and other parts requires high-precision cutting tools. The milling cutter made of M42 high-speed steel strip can maintain a sharp blade during high-speed cutting, accurately mill the complex cavity of the cylinder, ensure the processing accuracy reaches the micron level, and meet the strict requirements of the engine for the accuracy of parts. At the same time, its excellent wear resistance greatly extends the service life of the milling cutter, reduces the frequency of tool replacement, improves production efficiency, and reduces production costs.
In the machinery manufacturing industry, drills and taps made of M42 high-speed steel strips also perform well in the processing of various shafts, gears and other parts. When drilling high-strength alloy steel, M42 high-speed steel drills can easily penetrate the material and maintain stable drilling accuracy and dimensional tolerances during long-term continuous operation. When processing threads, the high hardness and wear resistance of taps can ensure the accuracy and surface quality of the threads and improve the assembly performance of parts.
(II) Mold manufacturing: guarantee of precision molding
Mold manufacturing is an important part of the manufacturing industry and plays a decisive role in product quality and production efficiency. M42 high-speed steel strip has demonstrated excellent performance in the field of mold manufacturing, providing a solid guarantee for the manufacture of precision molds.
In plastic mold manufacturing, for some plastic products with complex shapes and high precision requirements, such as mobile phone shells, automotive interior parts, etc., molds made of M42 high-speed steel strips can accurately replicate the shape and details of the products. Its high hardness and wear resistance make the molds less prone to wear and deformation during the long injection process, ensuring the dimensional accuracy and surface quality of plastic products. At the same time, the good cutting performance of M42 high-speed steel strips makes mold processing easier and can meet the processing requirements of complex molds.
In the manufacturing of die-casting molds, M42 high-speed steel strips are an indispensable material. During the die-casting process, the mold needs to withstand high temperature, high pressure and high-speed molten metal, which places extremely high demands on the performance of the mold material. The thermal stability and wear resistance of M42 high-speed steel strips enable it to maintain stable performance in such harsh working environments and extend the service life of the mold. For example, in the die-casting production of automotive aluminum alloy wheels, die-casting molds made of M42 high-speed steel strips can produce wheel products with high surface quality and stable dimensional accuracy, improving the production efficiency and quality of automotive wheels.
3. The key role of other areas
Aerospace : The aerospace field has extremely stringent requirements on the performance of materials. M42 high-speed steel strip plays a key role in this field with its excellent comprehensive performance. In the manufacture of aircraft engines, M42 high-speed steel strip is used to manufacture key components such as turbine blades and turbine disks. These components need to withstand high temperatures, high pressures and huge centrifugal forces when the engine is running at high speeds. The high hardness, thermal stability and wear resistance of M42 high-speed steel strip can ensure that they work normally under extreme working conditions and ensure the reliability and safety of the engine. At the same time, its good processing performance also enables parts with complex shapes to be manufactured through precision processing, meeting the high-precision requirements of parts in the aerospace field.
Automobile manufacturing : In the automobile manufacturing process, in addition to the cutting tools and mold applications mentioned above, M42 high-speed steel strips are also used to manufacture some special automobile parts. For example, the engine valve spring seat of the automobile needs to work in a high temperature and high load environment. The high strength and wear resistance of M42 high-speed steel strips enable it to withstand the frequent impact and vibration of the spring and ensure the normal operation of the valve. In addition, in the manufacturing of automobile transmission gears, M42 high-speed steel strips can also be used to manufacture some high-precision gear tools to ensure the processing accuracy and quality of the gears and improve the performance and reliability of the transmission.
Electronic equipment manufacturing : With the miniaturization and precision development of electronic equipment, the requirements for the processing accuracy of parts are getting higher and higher. Micro-tools made of M42 high-speed steel strips, such as micro-milling cutters and micro-drills, play an important role in the processing of electronic equipment parts. In the manufacturing process of mobile phone motherboards, tiny circuit boards need to be precisely processed. Micro-milling cutters made of M42 high-speed steel strips can perform precise milling operations in a tiny space to ensure the accuracy and quality of circuit boards. At the same time, its high hardness and wear resistance also make the tool less likely to wear during long-term processing, improving processing efficiency and product consistency.
3. Production process of M42 high speed steel strip
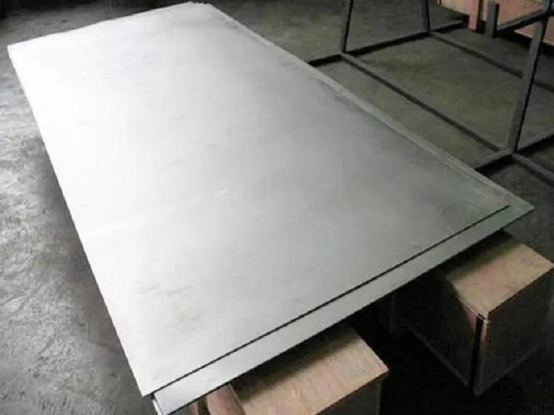
1. Process and key points of traditional craftsmanship
The traditional production process of M42 high-speed steel strip is a rigorous and complex process, in which each link is closely linked and plays a decisive role in the quality of the final product.
Melting : Melting is the starting point of M42 high-speed steel strip production. Its purpose is to fuse various raw materials in precise proportions to obtain molten steel with uniform chemical composition and in compliance with standards. In this process, high-quality scrap steel, pure metals and various alloying elements are accurately measured and put into an arc furnace or induction furnace. The high temperature generated by the strong current causes these raw materials to melt rapidly and mix thoroughly. During the smelting process, the temperature and time need to be strictly controlled to ensure that various elements are evenly dissolved in the molten steel. At the same time, the chemical composition should be closely monitored. The content of carbon, molybdenum, cobalt, chromium and other elements in the molten steel should be detected in real time through spectral analysis and other means. Once the composition deviation is found, it should be adjusted immediately to ensure that the chemical composition of the molten steel meets the standard requirements of M42 high-speed steel. For example, in the production of a large steel enterprise, the advanced automatic control system can accurately control the carbon content within the range of 0.90% – 1.05%, ensuring the stability of the molten steel composition.
Casting : The qualified molten steel obtained after smelting is then cast into a specific mold and solidified into an ingot or continuous casting billet with a certain shape and size. In the casting process, the control of the cooling rate is crucial. If the cooling rate is too fast, greater stress will be generated inside the ingot, resulting in defects such as cracks; while if the cooling rate is too slow, it will affect production efficiency and may cause uneven microstructure of the ingot. In order to obtain good casting quality, water cooling or air cooling is usually used to control the cooling rate. At the same time, during the casting process, it is necessary to ensure that the flow of the molten steel is smooth, avoid turbulence and gas inclusions, so as to ensure the internal quality of the ingot. For example, in some advanced casting production lines, electromagnetic stirring technology is used to make the molten steel more uniform during the solidification process, reducing the occurrence of internal defects.
Forging : Forging is a key process to improve the structure and performance of M42 high-speed steel strip. The forging process can break up the coarse grains and carbides in the casting structure and make them more evenly distributed, thereby improving the strength, toughness and wear resistance of the steel strip. Before forging, the ingot or continuous casting billet needs to be heated to a suitable temperature range, generally 1000-1150℃. At this temperature, the steel has good plasticity and is easy to forge. During the forging process, through multiple upsetting and drawing operations, the steel is subjected to pressure in different directions, thereby achieving the purpose of refining the grains and improving the distribution of carbides. The control of upsetting ratio and drawing ratio is crucial to the forging quality. Generally, the upsetting ratio should be above 3, and the drawing ratio should be reasonably adjusted according to the specific product requirements. For example, when manufacturing high-performance M42 high-speed steel tools, by accurately controlling the forging process parameters, the distribution of carbides can be made more uniform, and the cutting performance and service life of the tool can be improved. After forging, the steel needs to be cooled slowly to eliminate internal stress and prevent defects such as cracks.
2. Innovation and breakthroughs in modern technology
With the continuous advancement of science and technology, the production process of M42 high-speed steel strip is also continuously innovating and developing. Modern technology has made significant breakthroughs in improving production efficiency and optimizing product performance.
Powder metallurgy technology : Powder metallurgy technology is an important innovation in the production process of M42 high-speed steel strip. The traditional smelting and casting process is prone to problems such as carbide segregation during the production process, which affects the uniformity of the performance of the steel strip. Powder metallurgy technology is to make the raw materials of M42 high-speed steel into powder, and then press and sinter them under high temperature and high pressure to recombine the powder into a dense steel. In this process, carbides can be evenly distributed in the steel matrix, avoiding the problem of carbide segregation in traditional processes. Powder metallurgy technology can also produce M42 high-speed steel with a higher alloy content, further improving its performance. The hardness and wear resistance of M42 high-speed steel strip produced by powder metallurgy technology are 10% – 20% higher than those produced by traditional processes, and have been widely used in the field of high-end cutting tools and mold manufacturing.
Advanced heat treatment technology : Heat treatment is an indispensable part of the production process of M42 high-speed steel strip, which can further optimize the organization structure and performance of the steel strip. Modern advanced heat treatment technology has been innovated and improved on the basis of traditional processes. For example, vacuum heat treatment technology can heat and cool the steel strip in an oxygen-free environment, effectively avoiding problems such as oxidation and decarburization, and improving the surface quality and performance stability of the steel strip. In the vacuum heat treatment process, by precisely controlling parameters such as heating rate, holding time and cooling rate, the M42 high-speed steel strip can obtain a more uniform organization structure and good comprehensive performance. In addition, the application of new quenching processes such as isothermal quenching and graded quenching can also effectively improve the toughness and hardness of the steel strip and improve its fatigue resistance. In an aerospace parts manufacturing company, advanced vacuum heat treatment technology is used to treat the M42 high-speed steel strip, so that it can still maintain good performance under high temperature and high load working environment, meeting the strict requirements of the aerospace field for materials.
Online detection and quality control technology : In the production process of modern M42 high-speed steel strip, online detection and quality control technology plays an important role. Through advanced sensors and automated detection equipment, real-time monitoring and data collection can be carried out for each link in the production process. During the smelting process, the chemical composition of the molten steel is monitored in real time by a spectrometer; during the forging and rolling process, the thickness, width and surface quality of the steel strip are detected online by a laser thickness gauge and a profilometer; during the heat treatment process, the temperature is precisely controlled by a thermocouple and an infrared thermometer. Once an abnormal data is detected, the system will immediately issue an alarm and make adjustments through the automated control system to ensure the stability of product quality. At the same time, the use of big data analysis and artificial intelligence technology to analyze and process a large amount of data in the production process can predict equipment failures and product quality problems in advance, achieve preventive maintenance and quality optimization, and further improve production efficiency and product quality.
IV. Market Status and Future Trends
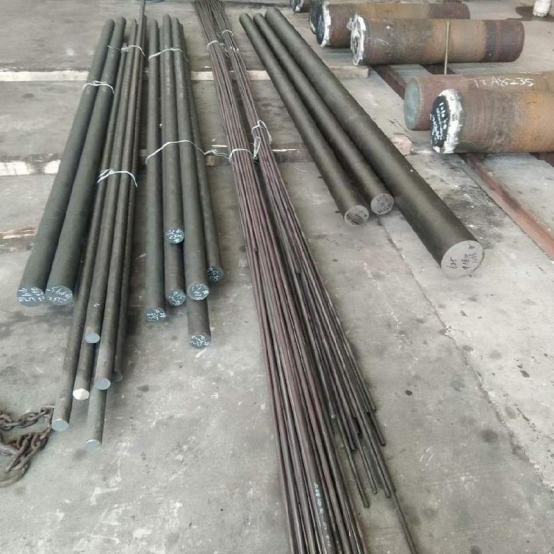
1. Market structure analysis
In the current M42 high-speed steel strip market, there is a diversified competitive situation. Internationally, some well-known steel companies have occupied a large market share with their advanced technology and excellent brand influence. As a global leader in metal processing and mining, Sandvik AB has strong strength in the production and sales of M42 high-speed steel strips. Its products are known for their high quality and high performance, and are widely used in high-end fields such as aerospace and automobile manufacturing, and have a high market share in the global market. Sweden’s Assab is also an important player in this field. The M42 high-speed steel strips it produces have a high reputation and market share in the European market, stable product quality, and outstanding performance in the fields of mold manufacturing and cutting tools.
In the domestic market, with the rapid development of the steel industry in recent years, some local companies have also emerged in the field of M42 high-speed steel strips. As a leading enterprise in the domestic tool industry, Shanghai Tool Works Co., Ltd. has invested a lot of resources in the research and development and production of M42 high-speed steel strips, and continuously improved product quality and performance. Its products are not only widely used in the domestic market, but also exported to many countries and regions, occupying a certain share in the domestic market. Tiangong International is also one of the important domestic manufacturers of M42 high-speed steel strips. The company has advanced production equipment and technology, a rich product range, and can meet the needs of different customers. It has strong competitiveness in the domestic market.
In the market competition, price, quality and technological innovation are the key factors for enterprise competition. Some large enterprises have certain competitiveness in price by virtue of their scale advantages and cost control capabilities; while some enterprises meet the needs of high-end customers by continuously improving product quality and technological innovation, and gain a foothold in the market with differentiated competition strategies. Some enterprises improve the performance and quality stability of M42 high-speed steel strips by developing new production processes, thereby gaining higher added value and market share in the market.
2. Demand Forecast and Development Direction
With the continuous development and upgrading of the global manufacturing industry, the market demand for M42 high-speed steel strip is expected to maintain steady growth in the future. In the aerospace field, with the continuous advancement of aircraft manufacturing technology, the demand for high-performance materials is increasing. As a key material for manufacturing aircraft engine parts and aviation molds, the demand for M42 high-speed steel strip will continue to grow with the development of the aerospace industry. It is expected that in the next few years, the demand for M42 high-speed steel strip in the aerospace field will grow at an annual rate of 5% – 8%.
In the field of automobile manufacturing, with the development trend of lightweight and intelligent automobiles, the performance and precision requirements of parts are getting higher and higher. M42 high-speed steel strips are important in the manufacturing of key parts such as automobile engines and transmissions. With the steady growth of automobile production and the continuous upgrading of automobile parts manufacturing technology, the demand for M42 high-speed steel strips in the automobile manufacturing field will also show an upward trend, with an estimated annual growth rate of about 3% – 5%.
With the continuous advancement of science and technology, M42 high-speed steel strips will also develop in the direction of high performance, high precision and green environmental protection driven by new technologies. In terms of high performance, by further optimizing the chemical composition and production process, the hardness, wear resistance and thermal stability of M42 high-speed steel strips are improved, so that they can meet more complex and more stringent working conditions. In terms of high precision, advanced processing technology and testing equipment are used to improve the dimensional accuracy and surface quality of the steel strips to meet the demand for high-precision materials in fields such as precision machining and electronic equipment manufacturing. In terms of green environmental protection, more environmentally friendly production processes are developed to reduce energy consumption and pollutant emissions in the production process and achieve sustainable development.
M42 high-speed steel belt plays an important role in industrial development with its excellent performance and wide application fields. With the continuous changes in market demand and continuous technological innovation, M42 high-speed steel belt will usher in a broader development space and make greater contributions to promoting the upgrading and progress of the global manufacturing industry.
5. Usage and maintenance tips

1. Reasonable use to achieve optimal performance
When using M42 high-speed steel strip products, choosing the right tool structure and parameters according to different application scenarios is the key to fully exerting its performance. In metal cutting, if rough machining is performed on alloy steel with higher hardness, larger tool rake angles and clearance angles can be selected to reduce cutting force and tool wear and improve cutting efficiency. For fine machining, a smaller tool angle should be selected to ensure machining accuracy and surface quality. At the same time, the selection of cutting speed and feed rate is also crucial. When cutting ordinary steel, the cutting speed can be controlled at 80-120m/min and the feed rate is 0.1-0.3mm/r; when cutting difficult-to-machine materials such as stainless steel, the cutting speed should be appropriately reduced to 50-80m/min, and the feed rate should be reduced to 0.05-0.2mm/r accordingly, which can not only ensure the service life of the tool, but also achieve efficient machining.
In mold manufacturing, for stamping dies, the appropriate mold gap and blade shape should be selected according to the thickness and hardness of the stamping material. For thinner materials with lower hardness, the mold gap can be appropriately reduced to ensure the accuracy and quality of the stamped parts; while for thicker materials with higher hardness, the mold gap needs to be appropriately increased to prevent the mold from being damaged due to excessive force. The blade shape should also be reasonably designed according to the shape and requirements of the stamping parts to improve the service life of the mold and stamping efficiency.
(II) Regular maintenance to extend service life
Regular care and maintenance are important measures to extend the service life of M42 high-speed steel strip products. During use, the tool and mold should be cleaned regularly to remove surface chips, oil stains and other impurities. For cutting tools, the surface chips can be blown away with compressed air after each use, and then wiped clean with a clean cloth. For molds, special mold cleaning agents can be used for cleaning, and they should be wiped dry in time after cleaning to prevent rust.
If the tool or mold surface is found to be damaged by wear, chipping, etc., it should be repaired in time. For minor wear, it can be repaired by grinding or polishing to restore its cutting performance and surface quality. For more serious damage, such as large chipping of the tool or cracks in the mold, it should be repaired by welding, inserting, etc. During the repair process, it is necessary to pay attention to the selection of appropriate repair materials and processes to ensure that the repaired tools and molds can meet the use requirements. In addition, M42 high-speed steel strip products should be regularly treated with anti-rust treatment, which can be applied with anti-rust oil or anti-rust coating to prevent rust during storage and use.
Summary: The value and prospects of M42 high-speed steel strip
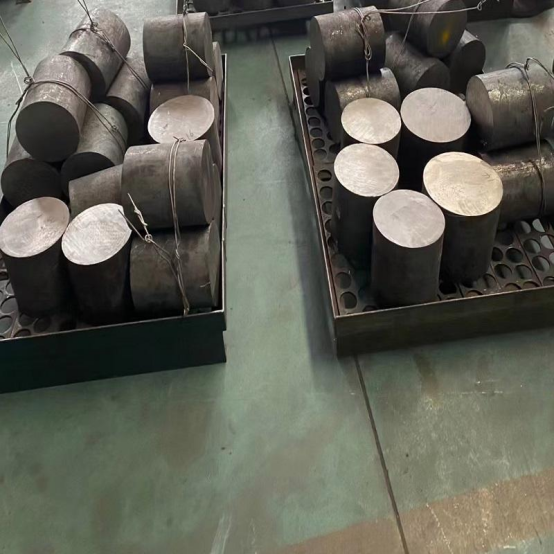
As a key material in the industrial field, M42 high-speed steel strip plays an irreplaceable role in many fields such as cutting tools, mold manufacturing, aerospace, etc. with its unique chemical composition and excellent performance. Its high hardness, good thermal stability, excellent wear resistance and cutting stability provide a solid guarantee for the high efficiency, precision and stability of industrial production.
From the perspective of the market structure, the M42 high-speed steel strip market presents a diversified competition trend, with domestic and foreign companies competing fiercely in terms of technology, quality and price. With the continuous upgrading of the global manufacturing industry and the continuous advancement of science and technology, the market demand for M42 high-speed steel strip is expected to continue to grow, especially in high-end fields such as aerospace and automobile manufacturing.
In the future development, M42 high-speed steel strip will continue to move towards high performance, high precision and green environmental protection. Through technological innovation and process optimization, its performance will be further improved to meet more complex and more stringent industrial needs; with the help of advanced processing technology and testing equipment, higher precision and quality control will be achieved; at the same time, we will focus on green environmental protection, develop more environmentally friendly production processes, reduce the impact on the environment, and achieve sustainable development. I believe that in the future, M42 high-speed steel strip will continue to play an important role in industrial development and make greater contributions to promoting the progress of the global manufacturing industry.
Add comment